UniForce Hydraulic Downpressure
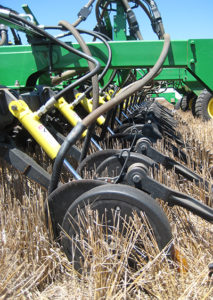
Get your JD 50/60/90/Pro-series drill to work the way it should!
- Reduce/eliminate hairpinning
- Get consistent depth!
- Better use of frame weight (& less frame stress)
- Less sidewall compaction
- Avoid misplaced seeds from sidewall blowout (gauge whls riding up)
- Greater upstroke/downstroke on openers than OEM
- Perfectly uniform pressure on all openers
Call 785-820-8000 to order
The biggest downfall of the JD 50/60/90/Pro-series drills is how down-force is applied—the rockshaft twists to compress a big coil spring on each opener. Because the spring is nearly parallel to the arm, the opener has almost no down-stroke—i.e., the spring is in the optimum position (applying the correct amount of down-force) for only about 1/4″ of its range. Had the spring been oriented differently (e.g., pushing straight down), the problem wouldn’t be nearly so bad.
So, you must have fields that are laser level for these openers to work correctly. Even 1/2” depressions give them fits. The spring starts to relax as the opener goes into these miniscule depressions, and you lose down-force—the opener loses depth, and starts hairpinning. To compensate, everyone cranks the pressure way up—so that the majority of openers have far too much pressure, just to keep those passing thru mild depressions working halfway decent. You end up with excessive sidewall compaction on most of the rows, while some aren’t even holding depth. Not to mention it takes a bunch of extra ballast on the frame. For this reason, it’s much more important to get rid of downpressure springs on these drills than it is on planters with a parallel link.
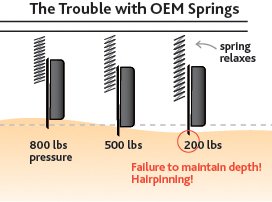
The Trouble With OEM Springs
The big coil spring on JD 50/60/90/Pro-series drill openers is a major downfall of that design. If the spring relaxes when the opener goes into the slightest depression, it loses down-pressure and fails to cut the straw & stalks (hairpinning!), and the furrow may be shallower if soil is hard.
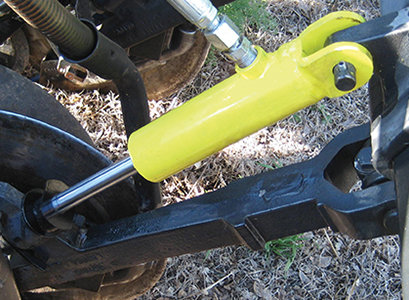
Single-Action cylinders
Maintain a completely uniform pressure across all the openers of the drill.
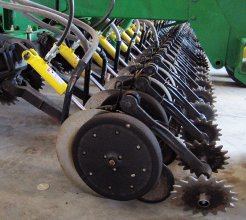
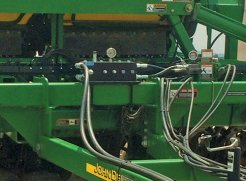
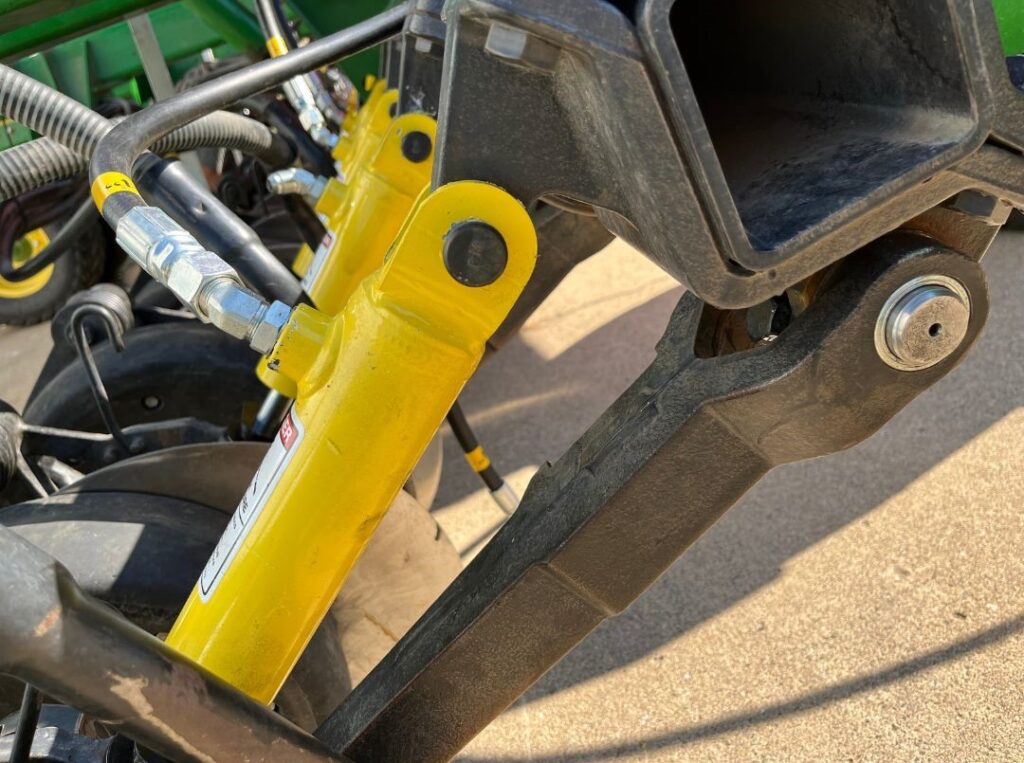
UniForce Hydraulic Down-Pressure
Our UniForce hydraulic system fixes Deere’s design debacle. Now, you can get uniform pressure on every single opener throughout its full stroke. The result is much better cutting, less hairpinning, holding depth much more accurately, and far less sidewall compaction. Another problem with springs is that they bounce: Hydraulics don’t have this problem. When developing the UniForce, we’d often leave at least one opener with the OEM spring. Watching them run side by side, it’s amazing how much the row(s) with OEM springs bounce, whereas the rows with UniForce are smooth and steady.
UniForce uses single-action cylinders along with the OEM rockshaft, which is still used to raise and lower the openers. The two hydraulic circuits may be plumbed together so that everything runs on a single tractor remote*, or they may be kept completely separate (two tractor remotes are used). *We prefer them kept separate.
Large 3/4″ header hoses* allow oil to move quickly from one end of the drill to the other, and between the front & back ranks. This keeps pressure almost perfectly constant even while going over steep terraces or through swales at high speed. Special brackets support the header hose on most air drill sections. Large 1/2″ drop hoses let oil move in & out of cylinders very rapidly. But don’t be fooled by the size of the hoses: The flow requirements are relatively low—for 48 rows, the UniForce takes only 4 – 8 GPM (for comparison, the air cart fan needs 25 – 30 GPM). (*Box drills use 1/2″ header hoses.)
Call for UniForce pricing and receive a free quote. All of our Exapta team members have hands-on experience with UniForce. They can answer your questions and work up a quote for you.
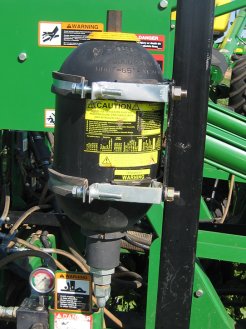
Optional Accumulator
For those who farm in terraces, especially when using only a single rank of openers, Exapta offers an optional 2.5-gallon accumulator for the UniForce system (JD 50/60/90/Pro) on air drills, or a pair of 1-gallon accumulators for a pair of box drills towed together on a hitch. When hitting terraces square-on, even the largest-capacity tractors can’t supply enough oil flow to keep the pressure constant, but our accumulator improves this considerably. (If you don’t farm in terraces, you don’t need an accumulator.)
*Includes brackets, hoses, fittings*
UniForce Hydraulic Downpressure System Testimonials
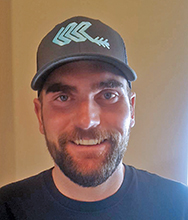
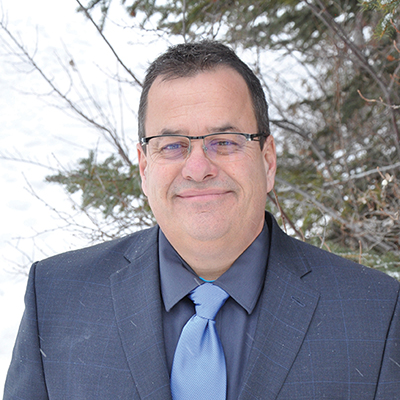
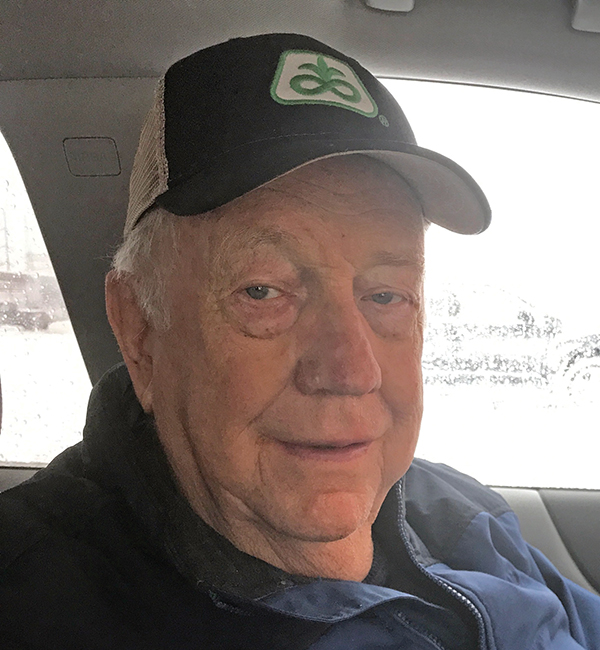
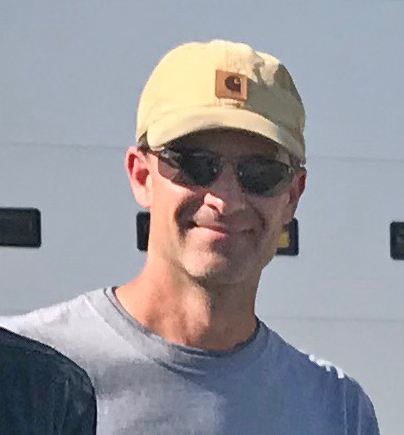
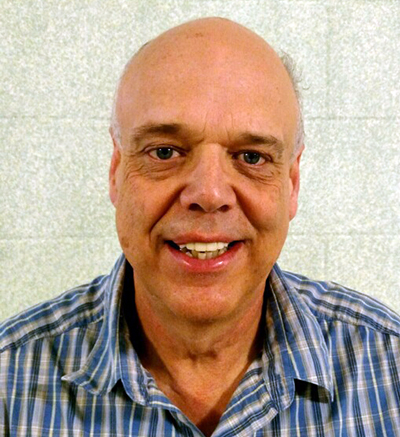
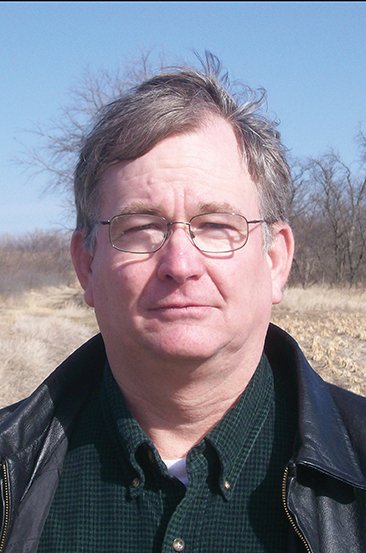
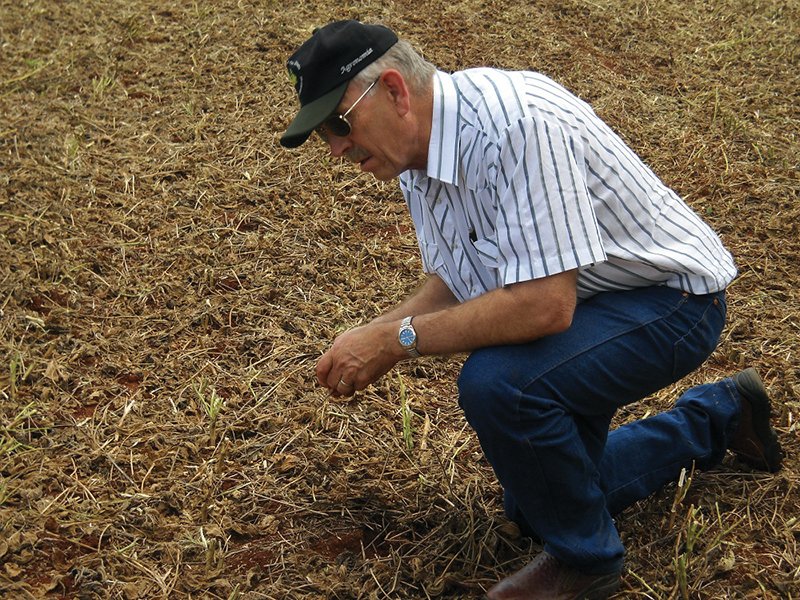
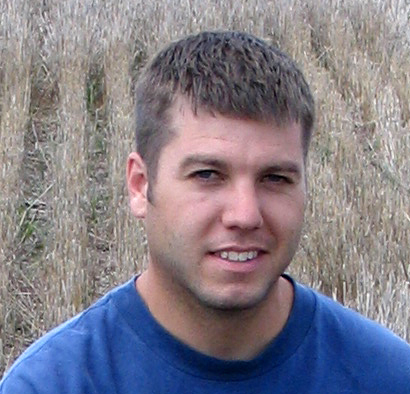
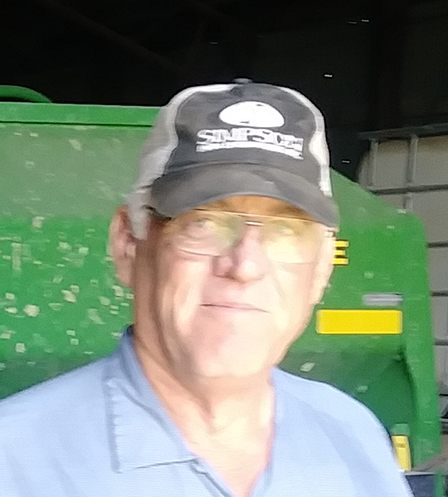
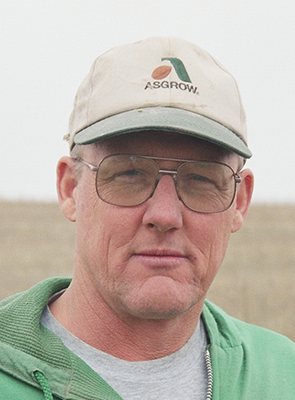
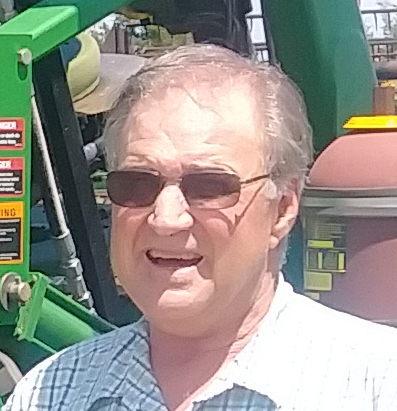
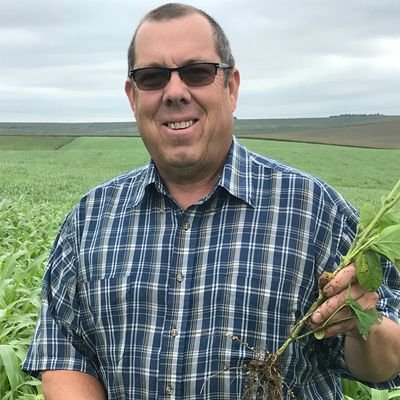
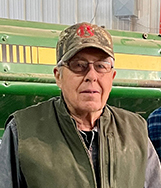
UniForce Hydraulic Downpressure Videos
See the UniForce system in action
Installing cylinders for UniForce Hydraulic Down-pressure system
About the UniForce Hydraulic Down-pressure system
In the News
Don Titlon shares with No-Till Farmer about his experience with UniForce. Read more.
Exapta Solutions’ new UniForce hydraulic down-force replaces the OEM springs on each opener with hydraulic cylinders to apply uniform force to the opener throughout its range of travel, for greatly reduced hairpinning of residue and much better holding of opener depth. Read More
Tom Cannon shares with No-Till Farmer that the Exapta upgrades to his drill including UniForce allowed him to lower his soybean seeding rate from 150,000 seeds down to 100,000! That’s a third lower seeding rate! As Tom stated, “That is a huge savings when you look at today’s high seed costs.” Read More
Downloadable Installation Instructions
- UniForce Air Drills 3-Section Single Rank CCS
- UniForce Air Drills 3-Section Dual rank CCS
- UniForce Air Drills 3-Section with Air Carts
- UniForce Air Drills 50ft
- UniForce Air Drills 60ft
- UniForce for Box Drills
- UniForce for Houck Hitches
- UniForce for Tow Between Carts
- UniForce Motorized Hydraulic Valve
- UniForce Troubleshooting Guide