Since gauge wheels determine the depth at which the openers penetrate the ground (assuming down pressure is adequate), it is of upmost importance that they are in good shape and don’t cause other issues.
The overall design of the gauge wheel has not changed in 50 years with a 16 x 4.5” wheel considered the standard size on planters and drills today. A wheel with too small diameter will not be able to ride over residue, whereas too large is constrained by room between the opener units.
Gauge wheels have been predominately rubber until recent years. As no-till has become more widespread, the need for compounds that can resist high-residue puncturing has brought poly tires into the picture. Polyurethane holds up so much better to sharp stubble with greater than 3x the life of rubber tires. This not only saves money over the seasons but also improves your seed accuracy by holding the integrity of the inner lip. In fact, the most important part of the gauge wheel is the inner lip. In addition to using a planter design that has the gauge wheel in the right place (to the rear of blade, where it exits the soil) the inner lip is what keeps the soil in place as the blade exits the ground. You need to have the wheel there to compact the soil to properly form the sidewall of the furrow. The furrow wall is the only thing guiding the seed into the center of the furrow. Moving to a poly tire, where the inner lip will last so much longer, will keep your furrows in check for the entire planting season.
You can see in these photos with the gauge wheel removed that there is no defined furrow. In the left pic you can see the seed is way off center under the sidewall. In the right pic you can also see the soil that stuck to the blade; if the gauge wheel was rubbing the blade clean, this would not happen.
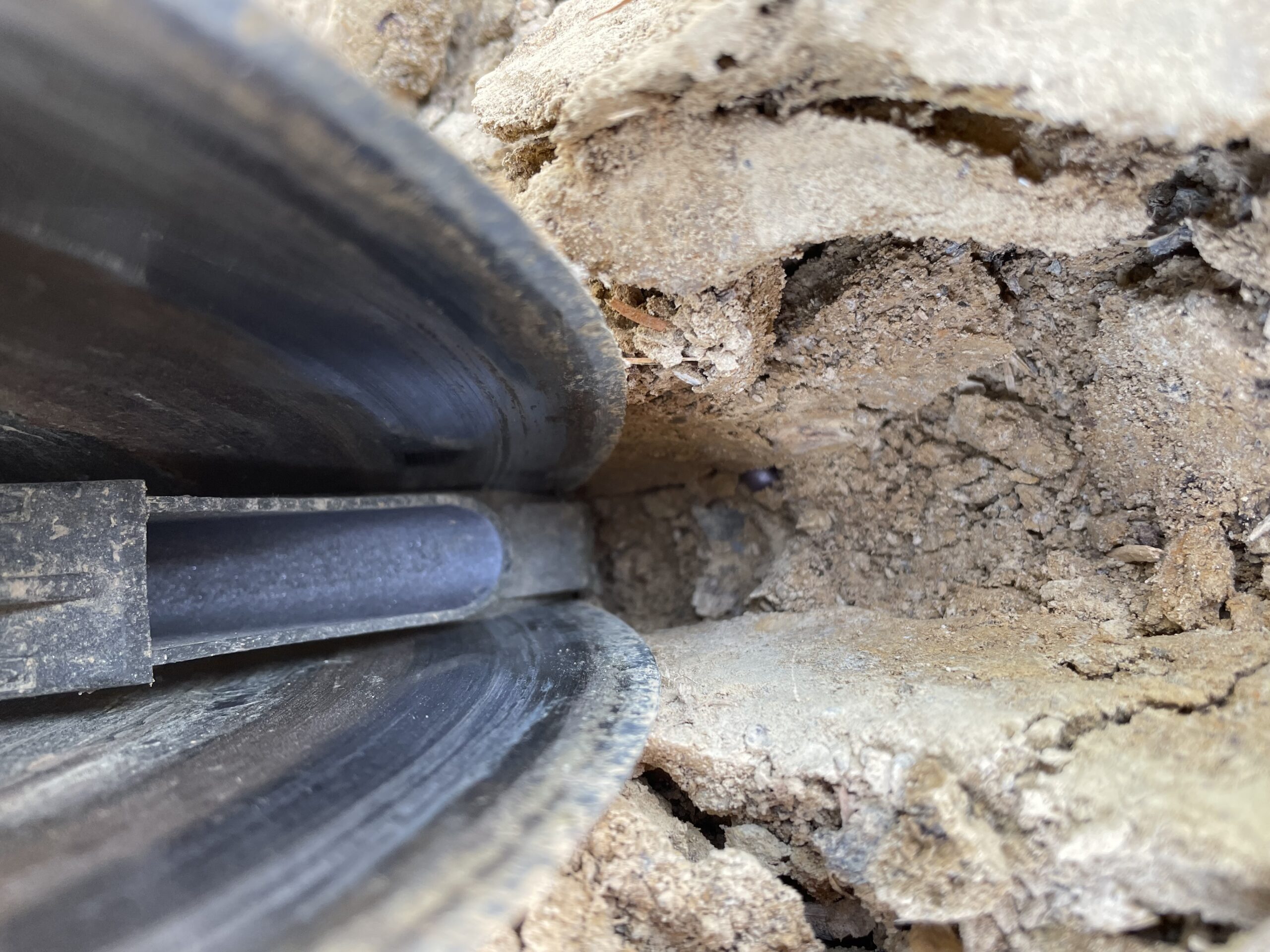
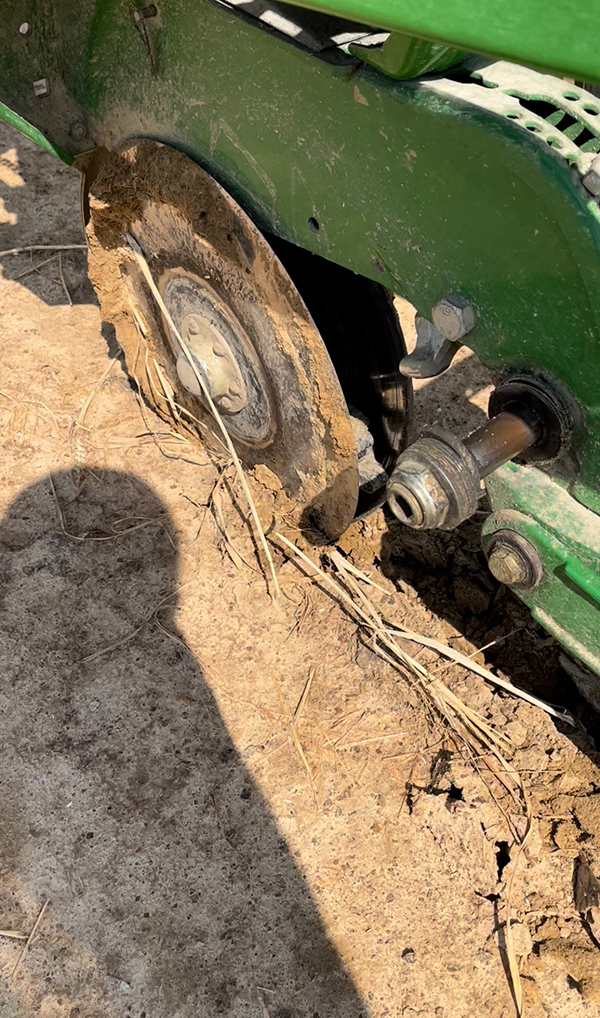
You’ll find wet soils can cause the gauge wheels to be problematic. Especially in sticky, wet soil conditions, the tires can build up with mud, causing the diameter of the tire to get larger, which then shallows up your planting depth. This problem gets worse when running poly tires as the current market offerings are rock solid with no flex to shed the mud. Another problem with wet soil is mud that gets thrown into the solid rim and cannot escape, packing the wheel full until it stops moving. Keep in mind these problems happen much more often in bare soil conditions; much less often when there is a good thatch of residue or cover crops over the soil surface acting as a barrier to mud buildup.
Planting in muddy conditions also brings up the question of spoked gauge wheels and are they worth it? The open spokes allow mud to fling out of the wheel, plus they are much easier to clean out if they do clog up. There are always a few wet spots in the field to mess the planter up and open spokes, allow quicker cleanup for less headache. If you have never had to clean out gauge wheels that clogged up, then open spoke rims really aren’t much of a need in normal planting conditions.
In dry conditions, where the soil is powdery, gauge wheels are essential for compacting the sidewall. They keep the furrow intact so the seed can reach the bottom of the trench, where the moisture is. Dry/powdery soil from the surface, falling in the furrow near the seed, can be a big contributor to uneven emergence. Chipped and punctured inner lips provide openings for the soil to remain loose instead of being compressed into the furrow wall.
There are different width gauge wheels offered. Narrow gauge tires are most popular on drills. The narrower row spacing runs over less residue which provides a smoother row unit ride. On planters you can plant closer to the old row (where the biology and fertility is) while also preserving that mulch cover needed to shade the soil. The only downside to going narrow is that the compaction gets moved closer to the sidewall. This will require more pressure on the closing wheels to close the row. Auto adjusting downforce systems help keep the pressure to only what is needed, which is especially helpful for sidewall compaction.
Keep in mind when it comes to sidewall compaction and consistent planting depth, the gauge wheel tires need to absorb all the obstacles the planting unit encounters in the field. Gauge tires that are rock solid will be excellent for wear life, but they will bounce over rocks and stalks in the field. The ideal gauge wheel would have flex to flatten out over obstacles but still have much better wear life than rubber tires. This difference in flex of gauge tires can go unnoticed when checking planting depth problems. Each tire will flex differently depending on the down pressure applied to that unit. A solid poly tire will not flex at low down pressures which can cause planting depth to be a little shallower than it was set at. Now I realize this is getting down to perfection, but in dry conditions especially, a half inch can mean that difference between moisture and dry soil. As always, double check your seed depth on each row in the field to make sure you’re accounting for these differences.
Exapta has brought to market the PolyFlex gauge wheel tire to avoid the issues above. It is a polyurethane tire that will outlast a rubber tire many times over, and it has an air cavity to give it some flex. The flex helps absorb all the bumps the wheels encounter in the field. This is important if you are trying to keep your planting depth even. Both our in-lab and in-field testing demonstrate flex that comes remarkably close to matching a rubber tire. By matching a rubber tire, your depth notches will be more accurate to factory settings. It is important to remember that tires that flex differently—or do not flex at all—will have a different planting depth even if you set the handle to 2”. Always double check rows in the field to account for differences (it’s not uncommon for different rows to be planting at slightly different depths).
Exapta will be offering the PolyFlex tire as a complete assembly on an open-spoke rim. If you’re looking for a ready-to-bolt-on assembly, our PolyFlex and spoked rim combo will make it quick and easy to realize these benefits.