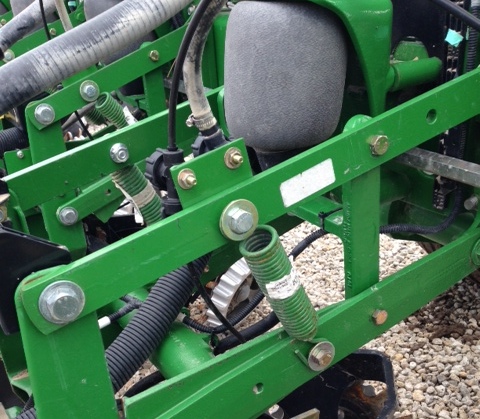
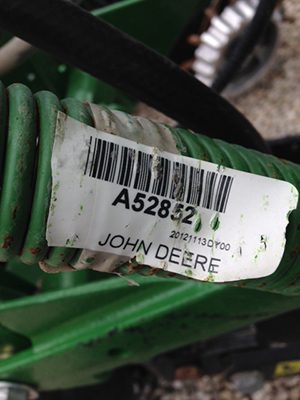
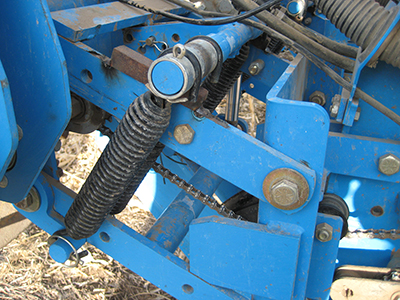
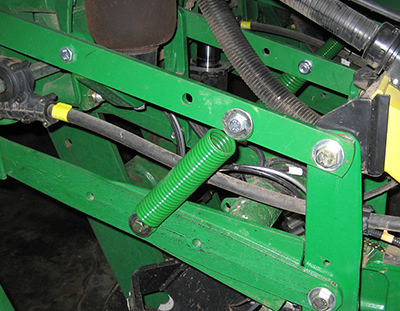
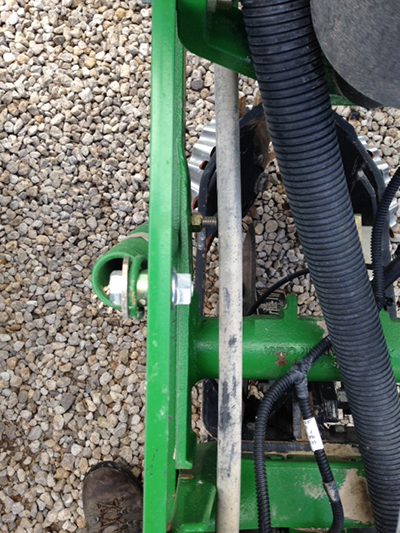

by Matt Hagny, consulting agronomist for no-till systems since ‘94.
With the planting season still fresh in your mind (unexplained variation in plant size? –any correlation to seed depth?), and with tougher planting conditions ahead if you are planting double-crops after wheat harvest in the southern half of USA, here are some tips on keeping enough down-pressure on the row unit of planters:
1) First, don’t rely on the down-force monitoring system to tell you if you have enough down-force. You can be badly misled. Always, always verify by excavating furrows in several different spots to determine actual depth being achieved by the opener blades, with the key being consistent depth in both moist soft areas, as well as harder, drier spots and/or combine tracks. At a minimum, the adjacent seeds should be at the same depth — i.e., the depth isn’t significantly different every few feet along any given row.
Many of the monitoring systems do a huge amount of data smoothing – so you have no idea that the openers are riding out much of the time unless you actually inspect the furrow.
2) You may find it quite necessary to add more down-force capability to the parallel-link. Even in moderate no-till conditions, down-force requirement to maintain consistent depth can easily exceed what air bags can supply. And sometimes even the modern heavy-duty down-pressure springs can’t do enough.
The solution is typically to add another 2 or 4 of the old-school springs to the parallel link (see photos). These react much more quickly than air bags, so they’re a big help on those systems. If additional springs are not easily installed, sometimes the quick-fix is to add more preload to the existing springs, such as by welding on some blocks (see photo).
Of course, these tricks only work if you’ve got enough toolbar weight – which is often lacking. To investigate this on air or hydraulic down-force systems, with the planter setting still, carefully measure whether the toolbar lifts at all when the down-force is engaged – i.e., as it goes from a very minimal amount to the maximum (this isn’t fool-proof, but it’s a good starting place).
For planters with mechanical springs only, the best way to check frame weight is by backing off the down-force on most of the row units on a planter section that’s loaded heavy (not the ends), but keep one row at max, then pull the planter a distance and compare the depth achieved on that one row vs what it was doing when all rows were maxed out — and looking in particular at the rows on the lightest section of toolbar. If there’s a difference in depth, you don’t have enough toolbar weight.
While excess down-force can be a hazard for sidewall compaction, in reality when I’m troubleshooting planters, 8 or 9 times out of 10 the down-force on the row unit is insufficient to maintain depth and hold the sidewall together — except perhaps in the mellower soils of the northeastern Corn Belt / Great Lakes region, or when it truly gets muddy.